140 - Development and implementation of the SBI test with Rudolf van Mierlo
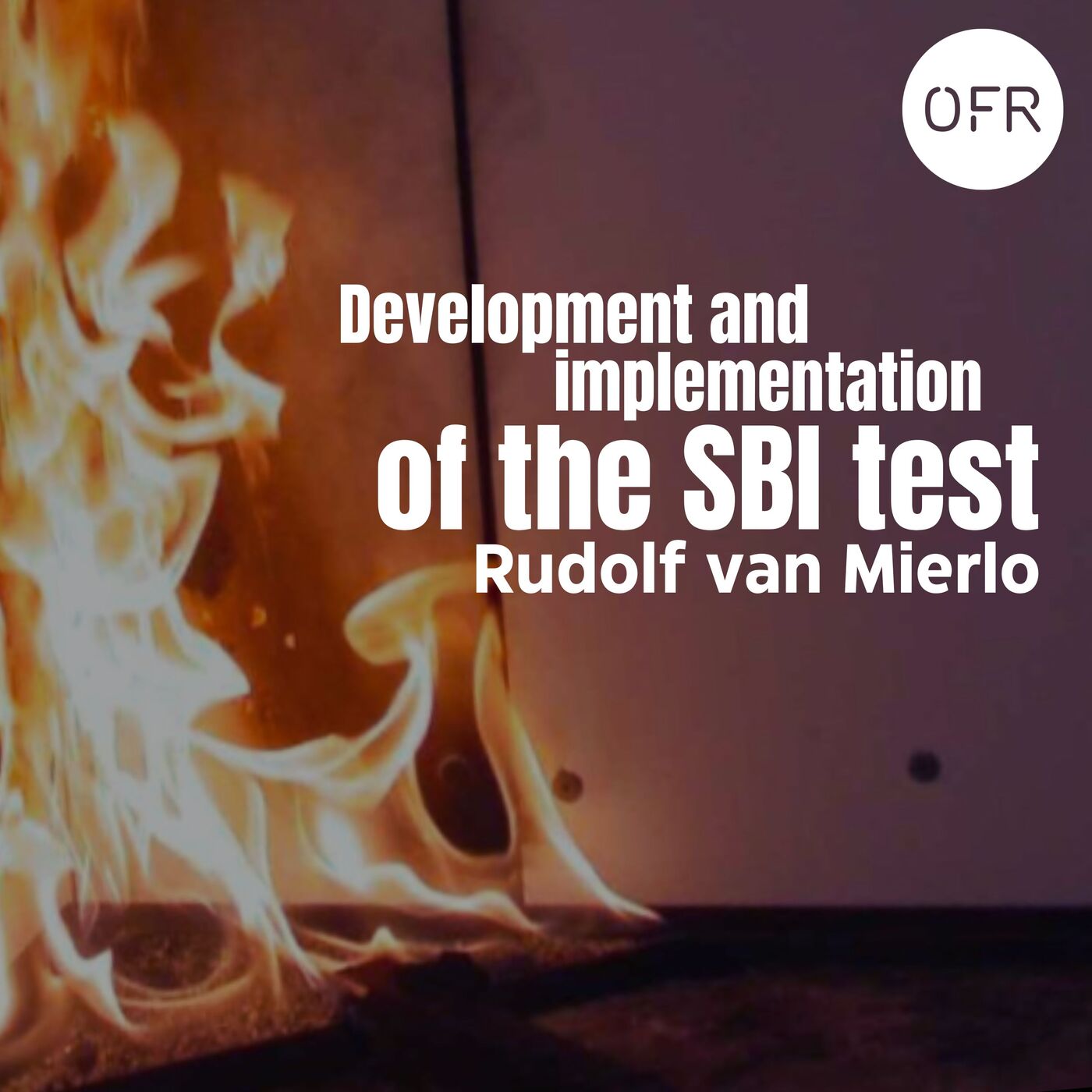
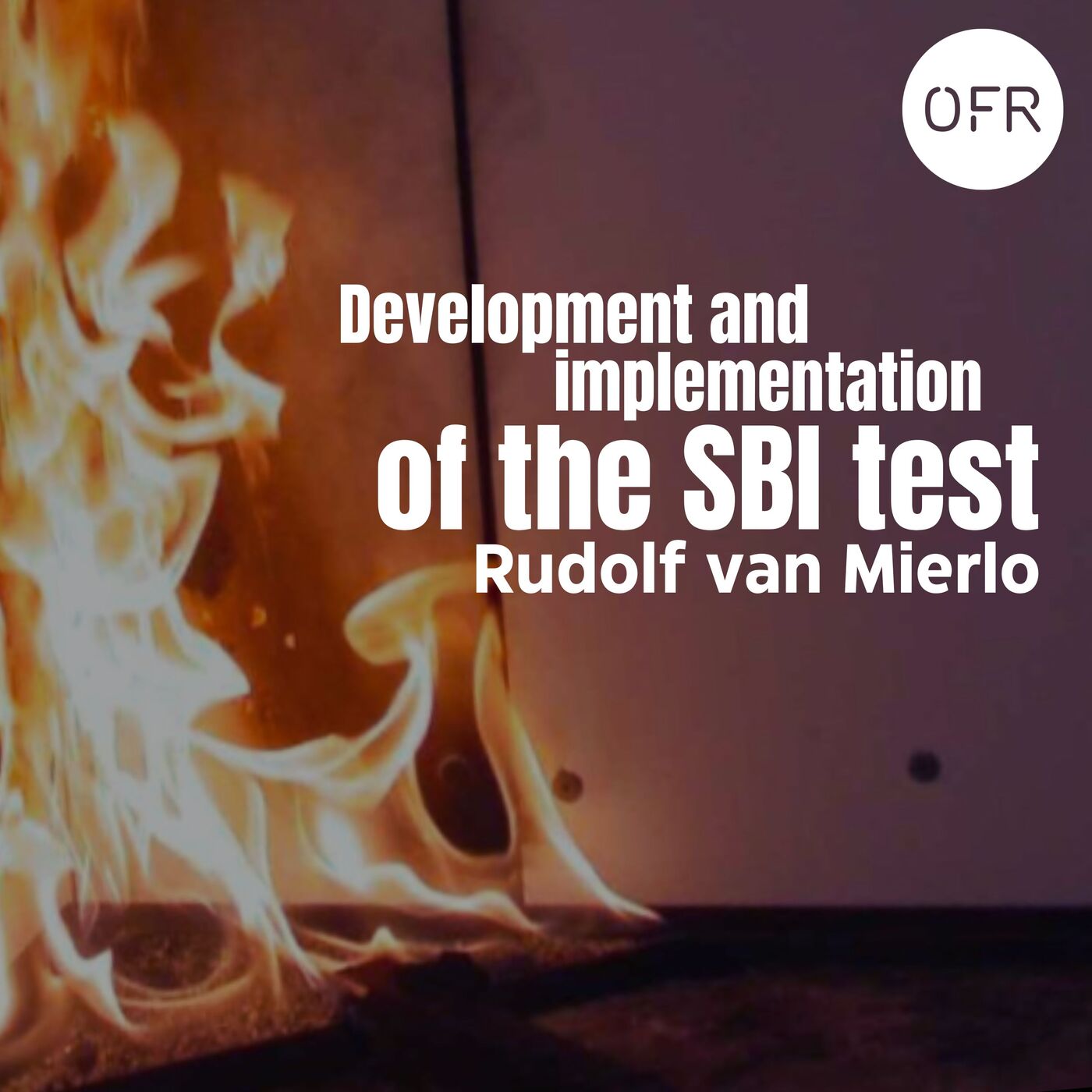
Tests in the world of reaction to fire are supposed to be representations of real fire scenarios, allowing us to grasp the characteristics of building products against them. While for the worst scenario (flashover fire) or the smallest ignition source (small flame), the definition is pretty straightforward. However, creating the intermediate method that the entire Europe would agree on was a bumpy ride. Our latest episode is a treasure trove of knowledge detailing the birth and maturation of the Single Burning Item (SBI, EN 13823 ) test standard. With the CEN SBI group Convenor - Rudolf van Mierlo, we discuss the history and background of the standard, the background for some not-so-easy technical decisions and perhaps even tougher political ones.
In a project of this magnitude, everything matters - how do you ensure the method is reproducible and repeatable? How do you convey the exact amount of information in the technical standard? Will one of the measures eventually be the one that defines the final classification, and what does the classification reflect?
Towards the end of the episode, we try to put those lessons from the creation and implementation of SBI into brainstorming a pathway for a new intermediate test we really need. An intermediate testing method for facades, as an effort for the Dutch government and a likely update to the existing ISO standard.
Reading material:
- The Rise of Euroclass by Angus Law et al. - a more detailed description of the politics behind the standard
- The Single Burning Item (SBI) Test Method - A Decade of Development and Plans for the Near Future by Rudolf van Mierlo and Bart Sette
- KRESNIK: A top-down, statistical approach to understand the fire performance of building facades using standard test data by Matt Bonner et al. - a more detailed description of how the Polish method handles different facades
Also, if you enjoyed this episode, you will like this one too: https://www.firescienceshow.com/089-designing-law-by-disasters-or-not-with-birgitte-messerschmidt/
Cover image - Effectis press release on changes to the SBI standard in 2020 - also a valuable source to see how the standard is evolving.
Hello everybody, welcome to the Fire Science Show. Today we have a big chunk of history of European Fire Safety Engineering and a bit of the future, a small step towards the future hopefully bright future of European Fire Safety Engineering. If you've read, I can say famous paper by Angus Loh and colleagues on the rise and rise of Euroclass system, it has painted an image of overly powerful group of people who are setting up the European legislation in terms of Euroclass a lot of politics and interesting background stories on how the Euroclass system was born. I've invited today one of those overly powerful people. His name is Rudolf van Mielow. He is with DJMR now. He was with Effectis and Tino back in the days and Rudolf was one of the drivers of implementation and development of the SBI, the Single Burning Item Test Standard, which is used all over the Europe to assess the middle Euroclasses for many, many products. In this podcast episode I have a chance to discuss the rise of the SBI standard with Rudolf. What was the background back then, in the day when the test was standard was developed? How did they approach it? What was driving the design choices behind the standard and how did it look to actually introduce a pan-European a truly pan-European standard method In practice. We're discussing the round-drop ins, we're discussing the calibrations, we're discussing challenges of introducing oxygen depletion calorimetry. So a lot of technical stuff, but also a bit of politics and a bit of kitchen how stuff like standards are developed. And for the future part, given 20 years of practical use of the SBI method, given all the experience with how the method was constructed and implemented, we take a look at the facades. We know that facades were next to be standardized, which kind of did not happen. Today we're working towards a pan-European large-scale test for facades. But Rudolf is bringing an important cause for an intermediate-scale method and towards the end of the episode we have a chance to discuss it a bit. So a lot of history, a bit of refreshing new thoughts. For me it was very interesting. I hope it will be as much for you. So, yeah, enough talking, let's spin the intro and jump into the episode. Welcome to the Firesize Show. My name is Vojci Węciński and I will be your host. This podcast is brought to you in collaboration with OFR Consultants. Ofr is the UK's leading Fires consultancy. Its globally established team has developed a reputation for preeminent fire engineering expertise, with colleagues working across the world to help protect people, property and environment. Established in the UK in 2016 as a startup business of two highly experienced fire engineering consultants, the business has grown phenomenally in just seven years, with offices across the country in seven locations, from Edinburgh to Bath, and now employing more than a hundred professionals. Colleagues are on a mission to continually explore the challenges that fire creates for clients and society, applying the best research, experience and diligence for effective, tailored fire safety solutions. In 2024, ofr will grow its team once more and is always keen to hear from industry professionals who would like to collaborate on fire safety futures. This year, get in touch at OFRConsultantscom. So hello everybody, welcome to the Firesize Show. I am today joined by Rudolf van Mielow from DGMR. Hello, rudolf, good to have you in the podcast. Hello, wojciech, and what a professional career you had. I know now you're with the DGMR, but I recognize your name from the years in TNO and I know you've been also a part of Effectus and it seems you've also been dealing with this overly powerful organization called EGOLF. I'm really happy to have you in the podcast because for a long time I have brainstormed how to approach the topic of European standardization over the single burning item tests and I know you've been kind of involved in that one.
Speaker 2:Yes, even more than a kind of involved, I think.
Speaker 1:That's what it was said in the recommendation letter. Anyway, because Patrice will kill me if we don't plug it very soon, I will be also very happy to meet you in person in a month from now, because we're meeting in the Netherlands for a very interesting conference held by the DGMR on 21st March at Zinger Museum in Lauren in the Netherlands. Let's maybe first plug in what's the conference about and what we're going to do there. Really happy to be there and speak about green façades in this event.
Speaker 2:It's a conference about partly fire safety and partly sustainable future, and especially the mix of those two, because we use more and more bio-based materials, especially insulation materials in façades, for instance, and of course there is also an influence on fire safety. My own presentation, with a colleague of mine, will be about the fire size, but you also hear several presentations of the more sustainable part.
Speaker 1:I saw the speaker line up. I'm a part of it. I'm looking forward to that conference. Even on sustainability in Slovenia at the end of last year was accident. I hope this one is as well. Anyway, let's go on to the topic. You have extensive history of basically building up the SBI standard and then implementing it, round-dropping, testing it. Then you had a chance to use the standard for many, many years. Now we're 20 years after it has been initially introduced to the market, used by many laboratories. We know the strengths, we know the downsides of the standard. I guess there's a lot of lessons for the future and it seems we struggle to define new pan-European standards. I am actually quite fascinated how a truly pan-European standard could have been developed. In the paper there's this sentence that no set of existing methods was both politically and technically acceptable. I would never have thought about political acceptance as a criterion for testing method, but perhaps that's the trick. So tell me, what did the landscape look like those 30 years ago when the effort was started on defining SBI, and why did we need a pan-European testing method?
Speaker 2:It's about barriers to trade. The reason why originally the CPD and later now the CPR developed is to take away barriers to trade, and for that it is important that… Wait, take away.
Speaker 1:Okay, take away. Take away from some, put on the way for others, I guess.
Speaker 2:Of course there are positive and negative in that, but the original reason was to take away barriers. It was not very uncommon. It was even common that if you did one test in one country, another country people didn't believe that that was enough proof. So you had to do the test again in their national laboratory and in the third country and the fourth country again. So it's not so easy to sell your products over the whole of Europe then. So we needed an harmonized test standard.
Speaker 1:That's just a clear reason. So Poland at that point was just outside of communism and we were still decades to go to join the EU. So I guess, comparing for example, poland and Netherlands, countries with completely different histories, even the forms of government were different. So you can expect that Polish standards would be vastly different than the Netherlands one. But you're in the heart of the Europe. You would say that, for example, products tested in Belgium would not be allowed in Netherlands or Germany.
Speaker 2:Yeah, it was a big difference what was allowed in one country and allowed in the other one. I think that the difficulties and a lot of people don't know that the performance of products, of facades or walls or floors or whatever, is very dependent on the fire scenario that you use. And actually the different test methods in the different countries use very different fire scenarios and different heat exposure, different radiation convection conduction. So if you compare the different national test methods there were, in one country a product would be good and in another country it would be bad. Of course there were also a lot of products that were good in most countries and bad in most countries, but there were also a lot of products that were very different, performed very different according to the national test method.
Speaker 1:And in terms of general trade, was it like today? The trade was free between the countries In European Union. You were a producer in Netherlands, you could sell to France. How did the barriers look there?
Speaker 2:You could sell everywhere, but you had to prove in every new country where you arrived that your product performed okay according to the national standards, and of course this is sort of barrier. And then even locally there was an additional barrier that a lot of local people stopped the product there because you had to test it again somewhere in a part of a country even.
Speaker 1:Okay, that's very interesting. I remember similar things happening in Poland when we were joining EU and how our system was, let's say, migrated into the Euroclass system. By the way, the Euroclass system that was developed much before the SBI. I've read in some of your papers that it was around 1993 that this Euroclass classification system where we assign the classes from A to F in the European system, A means the best, F means the worst, but tested In the outlook of the Euroclass method, there's a range of methods from small flame to a fully developed fire test and there was a need for an intermediate method. That's how I've read the origins. Why SBI efforts? How did the intermediate level look the moment you started working on SBI and what did you take to start with?
Speaker 2:Before the European system started the reaction to fire, several countries decided what the principal essential requirements were that a product should meet, and fire safety was one of them. Second level, what essential things in fire safety should be dealt with. And when that was decided, it was clear that the reaction to fire should be based on several scenarios. And then the discussion starts what scenario to use? At the top is clear a fully developed fire. What is the contribution in a fully developed fire? Ignition also clear. You use a small flame and that's the first start of a fire. Something in the between we could call it intermediate was an area where a lot of test methods existed, as I said, not correlating very well, and this is an end statement. So we needed one new test method. No, we needed one test method. It doesn't have to be new, but if you use a test method of one of the countries, there's a commercial positive effect for that country, and every country, especially the bigger countries, wanted there to see something that's equal or nearly equal of what they had before, and so there was a decision to make a new test.
Speaker 1:So everyone is in the same bed position. You're talking countries, but was it really truly a country representation, as in governments, or perhaps that was representations of industry, like who are people that were deciding In?
Speaker 2:principle, be aware. In principle, there were countries, there was a special group started, the fire regulators group, that had to discuss the issues about fire safety. But because most civil servants don't have in-depth knowledge about fire safety, most countries ask an expert in fire safety to come with them in the meetings and in fact, because it's such a specialized area, the experts had a lot of influence on the discussions and on the results.
Speaker 1:There's a paper by Angus.
Speaker 2:Yeah, yeah, yeah.
Speaker 1:It kind of goes into the fun parts of that process. Perhaps if the listeners have not read this paper, which should get some sort of like Pulitzer award for fire, then you should read to that. But let's focus on technicalities. So you had to base on something. What did you base it on? Did you have a method that was the closest to SBI and worked it? All the words? Or you have said, okay, we need a corner and let's start with the corner.
Speaker 2:Yeah, in principle we need a corner. Even that was not the principle. What fire is possible in small deans? And when you look in the room, when is the wall attacked most? That's in a corner position. So therefore, we started with a corner position in the small room as the scenario that we had to represent. Of course, on a smaller scale, it was possible to use a room corner test. That is a lane and it has a corner and it has a corner of course, but that is on a scale. You can use it, but the costs and the size and the costs.
Speaker 1:So room corners was 2.4 by 3.6 out of my head, if I'm not true 3.6, 2.4 and height also 2.4, 2.4 weeks and it requires you to line the entire room with the material. That's right. So that's? We're talking about like 20-something square meters of material that go per single iteration of the test. It takes like what an hour perhaps to run a corner, Depends how bad your material is.
Speaker 2:You are, but the time you need for the test is not so important. It's the time you need for installing everything and then taking everything out after the test. That's much more time than the test itself.
Speaker 1:So realistically, on a good lab you can do one a day, more or less, yeah, not more. Okay, you knew that corner setting, like in room corner, is kind of representative. In room corner we have significantly larger fire than SBIs. So how did you? Came up to the source 30 kilowatts in SBIs. You said it has to be representative of something.
Speaker 2:There were already tests in the different countries, especially the tests used in the larger countries. There was a lot of political pressure Depends of these test methods. In the SBIs, for instance, the maximum total heat flux of what is it around 40 kilowatts per square meter was not compulsory but was a goal. And that's exactly the maximum heat flux that is in the SBI just near the corner behind the flame. So it was developed in steps and a lot of steps. Of course, a radiating source also used. But if you need a radiation source that is producing 40 kilowatts per meter on a specimen, you need to place it very near the specimen. First, you can't see what happens with the specimen. Then that's one. Secondly, what happens when parts of the specimen come down or deform or whatever, and come against the radiating panel? That's not what you want.
Speaker 1:Yeah, okay, more details why it's closed in a small compartment box. It's a part of the standard. So, even as I've decided, we are closing it in some sort of compartment, right?
Speaker 2:Protection of a reparator nothing more, nothing less.
Speaker 1:Also, prevention of external effects like wind and stability of the.
Speaker 2:Yeah, that depends on where it is. Of course, in the laboratory Also, without that protection you can have very low speed of flows. But when in a small room you can organize that much better.
Speaker 1:Why no roof above the sample? That's another technical detail that's quite enriching, right.
Speaker 2:We investigated a small ceiling on top, but the results were then more variable and you then need, for instance, a larger hood. Well, there are a lot of practicalities to limit the size of the test method, gather good repeatability and reproducibility, and there are also more political and commercial reasons why a test is limited, because the costs grow when you take a bigger size of a test. So the ceiling was investigated but almost at a moment decided not to use it. But it's a bit silly, because a wall, a fire along a wall, is quite different from a fire against the ceiling.
Speaker 1:Yeah, of course, of course. I mean it's interesting, and perhaps few decades later, when the test is used for things that it perhaps was not perceived to be useful, it's interesting that those details are not there in place. I mean, in the end, right, I often say that fire testing is the science of logistics how to put as many samples and burn them efficiently in the lab without making too much mess. In here you've ended up with quite an elegant system. You open the back, you put a corner that's already built on two sheets of whatever material you use as the backing. You place them on a spot they fit. You don't install devices on it. You have the burner there already when the test is done. Open the back, throw it out, put the new one. Yeah, it's efficient, it's very efficient, I think in my lab. I'm not sure how many we can do, but I'm quite sure my colleagues could do a dozen in a day, at least on a long day.
Speaker 2:That is a bit difficult if the product gains because the temperature outside the test has to be. Yeah, sure, Very alone. Mr Schirru accepted.
Speaker 1:But still we are very far away from a single test that you could do in the room corner, and you perhaps don't need the firefighters' assistance for every single test you make. No, that's also a benefit. Sba method is not just the source, it's not just the compartment or the setup, it's also the measurements, and this test has heavily invested in oxygen-chlorimetry and other measures related to the production of smoke and toxic species of the fires. So tell me how that part was defined. How are you going to measure this fire?
Speaker 2:A very important starting point is to limit the number of visual observations. Of course. Many people that have experience in a laboratory know the endless discussions between different operators when viewing a test and viewing a specimen after a test. Were their flames consistently or just for a short time? Is this a piece of damage on that part, or is it not damaged but just soot? Or is it deformed or is it not? That's a rather terrible way of interpreting those results at the end. So we try to measure as much as possible. The oxygen-releasing method so counting the amount of oxygen molecules that has been used by the combustion, was a technique already there for two, three decades in the more research organizations and became more widely available for the labs. It was, and still is, a rather difficult method for new labs to cope with. That's clear, and that was one of the problems at the beginning. That was, for instance, quite clear in the first round, robin.
Speaker 1:In the 1990s, where you were implementing this or developing this, cold calorimetry was already a tool that was widely used, or I think cold calorimetry was also entering this sphere by then, right, it was only used by a few laboratories.
Speaker 2:As I said, more research-type organizations and less in the more commercial laboratories. And especially these laboratories. They had to introduce the oxygen-releasing method and the new SBI setup and do the first test in a very high-speed pressure cooker, because everything had to be done in a very short time. That was difficult in the first round, robin. That's why one of the reasons of that is that we did later that's, I think, a second round Robin.
Speaker 1:What was the reason for the speed? The European legislation, the need for the new method? What was driving it?
Speaker 2:The request for a new test method started six years before. So at the beginning and when the development went very, very slow, a lot of discussion and at a certain time the principles were agreed, the principles of a propane gas, vernier corner configuration. But then the standard has to be tested. Of course you need to know what repeatability and reproducibility is of a test method and whether all types of products give a sensible result in the test. You don't know beforehand. We now know what we can do and want to do with that method, but you don't know beforehand and the time was very limited. So I was the convener at that moment and I put a lot of pressure on the labs to produce results. If we had taken two years instead of half a year, maybe the quality would have been a bit better, but my experience more afterwards than before, that is that if you give the laboratories more time, they only start later. Sorry to say yeah, yeah, yeah, you're speaking truth, man.
Speaker 1:I agree, that's how it works. Everyone is busy and I know there was also a concurrent study in comparing SBI to Roomcorner, like using SBI kind of as a predictive way. What was it after the implementation, or was it already something that helped you define the method as itself?
Speaker 2:It has been done After that the European system had been built. But to get the right criteria, the class limits, comparison between the SBI and Roomcorner test results were used. But that was after the actual development of the SBI method. Then you can.
Speaker 1:So setting the levels of the ladder.
Speaker 2:Setting the levels, of course, commercial, very important criteria the limits for the different classes.
Speaker 1:Fantastic. So let's go back to the measurements. Can you briefly explain what is measured in the SBI and how? Mainly heat and smoke.
Speaker 2:Very simple Heat and smoke. Heat in the sense that the rate of heat release is measured and the speed of which the rate of heat actually grows at the beginning. At smoke the same, the amount of smoke and the speed of which the smoke is produced at the beginning and then a lateral flame spread to the end of the specimen. But that's nearly never, never important as a class decider. Going back to the first two, in heat the total heat release is in the first 10 minutes of the test. The test as a whole is 20 minutes and the speed of growth is in the FIGRA index fire index growth rate. And for the smoke the same. You have a total smoke production and the smoker also to smoke. In reality, both FIGRA and Total Eterlis can be the desired in a classification. It depends very much on the type of product. You know from certain products that the FIGRA will be decisive for the class and all the types of products. Whether THR will give the decision.
Speaker 1:Interesting because it will depend on, for example, material density, how much heat you can emit from lightweight material. You will eventually emit less heat than from the same material. Okay, if you have found material, it's going to weight less than the same material in solid form, but the rate might be much quicker. So I kind of like you know, separating the total production and the growth rates, how much in the end and what was the fastest rate it was burning. It's kind of interesting because it gives you two different point reviews. Was there any specific reason why a 10-minute window was chosen?
Speaker 2:Yeah, it was very basic. You need a good repeatability and reproducibility, especially in the second half of the test. The variation in, for instance, deforming, delamination and so on of the product causes a very large variation in results.
Speaker 1:so not so good repeatability and reproducibility, Okay, and now how to make sure that you burn a board out of polyethylene and you burn it in my lab. You burn it at TNO. How are we sure we are getting the same figure? Because it's quite sophisticated method of measurement. As you said, implementing oxygen calorimetry is challenging on its own, but here you also have some optical ways to measure smoke density for Smogra. So you have to capture the velocity in your duct. I mean to start off with. The ducts have to be the same in standardized. To what extent do you want to actually make sure that those tests are done the same in all labs?
Speaker 2:We started by producing the several SBI facilities one position at one place. So the apparatus then is the same and there are a lot of checks in the standard to know that, for instance, response time, delay time, are within certain boundaries. There are several calibrations exactly doing that, checking whether the system performs as required, especially the oxygen-replenient method.
Speaker 1:Okay, and then the most impressive part of this project for me, the round robins. So I mentioned there were two of them. Tell me what was the design principle of the round robins and how annoying that was the round robins itself.
Speaker 2:Round robins are often very annoying. If everything is new for everyone, you know that beforehand, so it will never produce an optimum result. Basically, what you measure is a repeatability, that is what the difference is between the same tests directly after each other at the same place by the same people, and reproducibility, which is different tests in different laboratories by different people on different apparatus. If these two have a small variation, then you know you have made a good standard. There is some special thing in it. You can't give too much instructions to people. Why not? Because the standard has to be self-explaining In the future. When you design the method then you think in the future people have to read the paper, the standard, and had to know what to do to do the test. And if an round robin instructs people what to do, that is additional information. Then you don't know what repeatability and reproducibility of that standard of paper is. So first you have to check the apparatus, whether everything is installed. You can see that we asked in several steps all the laboratories to send in their calibration results, for instance. We checked whether everything was okay and then they had to do the test on these large set of materials by themselves, without us telling what they should do better, or maybe it was okay what they did, but we couldn't give that instruction.
Speaker 1:Was it connected with accreditation process? You could promise them they will be accredited after that if they pass. No, no, no.
Speaker 2:You're not testing the laboratory, you are testing the method. Everything is done anonymous. So only the coordinator of the round robin knows afterwards in report which laboratory has produced what results. So you only see laboratory 8 producing this test results and laboratory 15 producing that test result.
Speaker 1:And to what extent the rigs were identical. Like were they built by the laboratories? Were there one supplier that supplied to the laboratory?
Speaker 2:There was one supplier. So that was the reason to limit that variability, not to ask people also to defend their own apparatus from the drawings. But it was produced, everything was producing, and that was the first set of SBIR apparatus. Of course afterwards there were two. I think there are two or three sources, main sources of SBIR apparatus.
Speaker 1:Super interesting, and the materials that were chosen were the representation of like the scatter across the euro classes, like from non combustible boards to like extremely flammable foams. How did you pick them?
Speaker 2:We tried to pick them as the products that would end up in the intermediate classes, but of course you don't know hard, so there were also a bit too good materials and a bit too low performing products, because you it's a new test method and you don't know where a product will end up. As I said before, the different test methods used in different countries produced very different results, so it's very difficult then to say what will be. The performance is in a quite new death method. We had an idea, but at the end it didn't end bad. I think there was a good spread over all the classes, but it could have been better, of course.
Speaker 1:So the repeatability was assessed in the end in how consistent was the class assigned to a product after the test? I guess Right? Or you were comparing those to the raw results like figuras, smogras of them.
Speaker 2:The NTT had the role to make all the repeatability and reproducibility calculations and these figures are produced then in the standard and one of the NXs. In the standard the repeatability and reproducibility is mentioned.
Speaker 1:Okay, now you have a time machine will leave 20 years after this is implemented. The entire Europe is using it. There's probably more than 50, maybe even 100, sbi rigs across the Europe being in a daily use. We've moved entirely into the Euroclass system, for good or bad. I don't know how do you view the process from today. Like I understand that you were working in a very specific circumstances time pressure and everything. Any fundamentally different decisions that would have been taken today if you had a chance to redo the process?
Speaker 2:I think a special requirement to produce the performance of a product in and use application is very, very difficult to do in practice. The range for that are very limited in the standards. You have a sort of a cafeteria behind that the product of 40 millimeters or 80 millimeters or whatever. I think that could have been done a bit better, but okay, you don't know by heart at that moment. Important is, I think that afterwards the SBI was used as the determining test in the mid classes for a lot of more five scenarios than in fact it gives good information, for instance at the Facades. Let me take one step back. Before the European system was developed, the important scenarios were selected. I think there were 12, 13, 14. And a few of them we see in the Euro classes. You have a fully developed fire, the A1, a2 tests, all non-compensability and color-reflexibility. At the bottom you have the small flame. In between you have a room corner and a corridor scenario. The corridor is only by radiation and that's a flooring test that's used for that scenario. But of course you have a facade, has a quite different combination of radiation conduction, convection. You have shafts, you have ceiling voids, you have staircases. In fact, to get optimum information about these scenarios. You need to do other tests, but in fact that would mean that the producer would have to do a lot of tests for all the scenarios, and that's what was not what intended. Your committee wanted to introduce a new system that was not a heavy burden for industry, so the number of scenarios was limited, and the first one to be added would have been facade. We discussed about that, as facade was left out, because nothing happens with facades.
Speaker 1:But we are talking about 1990s facades, right?
Speaker 2:We are talking about facades as they were built 30 years ago, not a facades we are building today. That will always be the case. We don't know what buildings we make in 20, 30 years, and maybe addition to test systems will be insufficient, because we know then that something else is very important. We don't know yet. That was the same 30 years ago.
Speaker 1:So, if I understand correctly, the SBI is good as it is, while it is used as intended and where it deviates more and more from the intended fire scenario that SBI represents as some source of fire in a compartment to a material that's predominantly a wall material. So let's say we go into a facade scenario. In facade scenario the way how you ignite facade is most likely through fires bending from your windows, like rolling over from compartment that is on fire onto the facade, or from a large external source like a trash or something that's stocked against the facade. In here it's not a flame touching the external surface of your system. It can be something that's actually attacking the cavity or the gap from between, from underneath the facade. I should be reading. It rolls out from the wind and we all understand the people who are doing the fire testing. We all understand that it introduces a completely different exposure to the thing tested. Even if you take the most simple case, take a piece of a paper and try to ignite it through the middle of the page, you can put a flame against the middle of a piece of a paper for a few seconds, but if you do the same to the edge of the paper, it will immediately catch fire. That's how ridiculously different those most of exposure are. So the fact that the material has achieved Euroclass B in SPI system is in no way an indication that it is material to be used in a facade environment. Before I let you go, even struggle in scenarios where you would also have a strong force ventilation flows. I had this issue in Poland in some tunneling projects where the lining of the tunnel for the creative means would be built from Euroclass B materials. I mean, that's great material, right? Euroclass B right, it's fantastic. But we're talking about a system where you have forced ventilation, high velocity flows, like completely different mode of heat transfer, then a free-standing flame in a compartment. It's a completely different setup, right yeah that's quite different.
Speaker 2:It's such a different setup that don't trust a B-class material. Be aware that B-class materials are good. In a room, corner configuration, there's also furniture, where there are also other things that can burn. Then there's another level of performance required. Then on a large facade or in a tunnel, there's a very good reason then to say this might be non-combustible or nearly non-combustible at a CY, a CY class A2 or A1.
Speaker 1:Yeah, but I'm bringing that as an example that the end use, the way where the product will be used and the fire scenario which will be the natural scenario for that product in that application in this particular building, is something that goes beyond what the project or whatever we are discussing here. It goes beyond a simple class. It's difficult to assess a number or a letter to a material and tell it whatever you do with it is going to be fine, right.
Speaker 2:Yeah, but be aware the examples we just used, for instance the tunnel you can use a higher class in the euro class system. Normally I wouldn't say that when I compare with lower classes, but the two highest classes are more material tests than tests. That end use is important. So non-combustible or nearly non-combustible is yeah. The euro class is a good representation of what you want with non-combustible.
Speaker 1:Yeah, sure, I mean, yeah right, it's difficult to design a bad product with non-combustible materials at all. Now so if we agree that the method we are discussing today, the SPI, is not perfectly representative for facade systems, we are currently ongoing through this definition of new pan-European standard for facade testing. Again, a very large testing methods, two countries that would like the method to look just like theirs, for reasons that you perhaps have mentioned in the beginning of the episode. I mean, it's kind of funny. It looks exactly the same like what you've said. But I know that, and it's something that you also brought to the table the need for an intermediate method. Again, we have material testing for the materials that are used in facades. We have the end-use full-scale large testing method. Again, the same issues long procedure, very costly. You can do only a few in a month. That's even more difficult threshold than room corner. It seems that the intermediate method would be very well received by the industry. What's your opinion on?
Speaker 2:that. Yeah, my opinion is that we need intermediate test methods. At the moment there are several countries that stepped from a B-class for all sorts of facade 10 years ago to an A2 class or a large-scale test, and then a large-scale in the sense of a British standard A414, part one, two, or the DIN German 4102, stroke 20. But that's the size that it tells me. This way, the SBIs is not a big test, but I know that in a lot of cases practical cases where you design a building, performing the SBIs test is already not so well fitting into the building process. Let's put it that way. So in the vast majority there is no test done on facades of a certain building, but it is compared with something that's nearly equal and it has a well, has a known class. If you introduce a BS test or a DIN test for every part of every building, then the cost will be enormous and that may be reasonable to ask for, but only in a high-risk situation, and there are a lot of situations in between. So if I look at what happened in Europe in the last 10 to 5 years a lot of countries changing their legislation to A2 or the real large-scale tests we did a research for our ministry, which would be something for the Netherlands to do, we couldn't find a good risk-based argument for that big step of performance. Those were political arguments, not risk-based arguments. So we propose in the Netherlands to the ministry to take a smaller step and have the other large test method to BS and the DIN as another possibility for maybe high-risk situations, but for the majority of situations to use an intermediate-scale test. And currently, as you know we talked earlier, we are developing an intermediate-scale test at the moment.
Speaker 1:There is this ISO test with a linear heat burner that is put directly underneath a piece of facade that's I don't know, 2 meters tall, in a corner configuration. I kind of like that test. It's actually quite brutal, to be honest, that test, and in Poland we have something that I would perhaps even consider an intermediate-scale. I think we always considered it as a full-scale test in Poland, but to the rest of the world it looks basically as an intermediate test, the one where we have 1.8 meter wide by 2.5 meter tall sample and we put a woodcrip against it and it's tested three times, each material three times, and it has wind component into it. So we're pushing the fire plume towards the facade through the wind and it's quite, I would say it fueled local certification. It was developed in Poland in 1980s in my institute, long before me, and till today it's still doing quite a good job in filtering out good from bad. You know it's. I mean I cannot quantify the fire behavior of a facade with that test to the level I could with BS test, for example. I don't have that much data from it, but I've never seen a material that would pass the Polish test and be extremely horrible in, you know, in larger test method, like I've never seen such thing and ventilated facades with combustible materials in them. They fail miserably in our test and you could use it like in Poland. It's used for giving classification to products, which is requirement by the local code, but I could see it being done as a screening test. You know you have you introduce a new material to the market. First material tests non combustible, combustible. Yes, we have combustible. Okay, here's your intermediate method. Let's see how bad the configuration is. It's not bad. Maybe you can stop. Then it looks dangerous. Okay, if you want to put it into the market, you need to have a proof from the full scale test. I think that's a quite reasonable pathway. What do you think?
Speaker 2:We choose the isotest you just mentioned, the 13 785 stroke one as a basis that we revised it considerably. I had a quick look at the Polish test and I can give you the reasons not to choose it. Okay, At that moment the isotest was our first choice. So I was looking for test methods that were better not the same performance. But and I had the impression that the Polish test wasn't that because of several reasons. First, the attack on the cavity, because the in a Polish test the woodcrip is in front of the facade, not under, and with an outer layer in the facade with hardly or no openings, the flame won't go into the cavity very fast and we wanted to have the exposure of the cavity at the bottom side, as if the flame comes out of a ring. Secondly, if there was a choice between an international test and a national test, we preferred an international test just to keep out discussions, to have one country in favor and not many other countries using the same method, and when you use or choose an ISO method you don't have that discussion and I was willing to start revising the method. As far as I know at the moment, they will follow completely or nearly completely what is now changed. They were revised by our Dutch project, because the major change we made is especially the oxygen-replenient method. I think that the more modern, the more sophisticated method produce more measured data. You can get much more about the performance of a product than by only visual observation or by temperature measurements. Even there were a few other things. A wood grip is not so constant in heat exposure as a guard so, and the Polish test had a wood grip so yeah, so I brought up the Polish, not as a proposal that should follow.
Speaker 1:I'm just giving an impression that an intermediate test can be in a country's low system for 40 years and be quite successful in fulfilling this particular role of being the filter of bad from good. In terms of our test I also there are parts I don't like from it. I don't like the grip for sure. I like ISO gas burner much more, and then it's definitely more reputable and it's easy. You can turn it off any moment you want. There is no uncertainty. Well, there is minimum uncertainty related to operation of the burner and the gas in Poland will be the same as in Finland and the same as in Spain. If you use propane, for example, and for a crib, we know that in our crib that's a small crib, but if you go into the BS crib inside BS compartment you can have from two to five megawatts with the exact same crib. That's massive. I like the wind as a boundary condition on the test, like. I think wind is something that really changes the outcome of the test. And what you said about cavities as long as there is a gap, as any vertical or horizontal gap, having wind present in the test. I find it quite reliable against ventilated façades. But wind prevents you from oxygen calorimetry and wind also introduces a new health and safety challenges in the lab. So if you subject the façade to the wind it's very difficult to collect all the smoke with the hood. So the smoke fills the entire compartment and it's quite big. So health and safety here, which we know is nasty, definitely a lot of space. I mean I'm very interested in the outcomes of what you propose to your government and I'm looking forward to seeing how we could internationalize that and where we could go. I think it's also something that could interest. Is there any? I assume it's your local country endeavor or is it related to the European Commission and the large testing method?
Speaker 2:No, we are now developing it in the Netherlands. But, as I told earlier, our proposals are also sent to ISO and they have been discussed in ISO, a working group too. But if I don't know whether people know what size it is, it's the same size as the Polish test, 2.4 meters high sample. It's a corner configuration, not flat, but a corner configuration 100 kilowatt burning line, burning under the large wing, Okay, and gas burner. So that gives a good idea. There are 10 thermocouples in the specimen, in the in front of the facade and in the cavity, and the most important thing is that the Hutter Buff. With the Hutter Buff we measure the oxygen with the oxygen depletion method. So you know to know the eaterlies.
Speaker 1:Very interesting development and I guess we'll be able to talk more about that on 21st March in Lauren, the conference for which everyone is invited, and for this discussion. Rudolf, it was a pleasure to have you in this show and perhaps some final words for the future designers of the test methods, Like one wise word of a person who developed and implemented what should they look for?
Speaker 2:Try to know and to get being informed about the background of test methods. What is it testing? Why is it tested that way? Because in a lot of cases in most cases even not the exact product as tested will be attached to a building, but something that's nearly equal and everyone should dive into. You get knowledge about what the influence is of these differences. It was only then, and then you will have safe buildings in practice Fantastic.
Speaker 1:Rudolf, thank you very much for coming to the Fire Science Show and I am looking forward to meeting person in Netherlands. Thanks, okay, okay, thank you, okay, thank you. Thank you, wojciech, and that's it. Thank you for listening. I hope you've enjoyed it. There is quite some reading resources for you if you wish. I've linked as soon as Angus Laws paper on the rise of the euro class, I've linked Rudolf's papers on the development of SPI and I've linked our Kresnik study on the Polish test method for FASA so you can take a look by yourself on how this looks in assessing performance over a large number of different FASAD samples. A lot of interesting things. And there's a chance to talk to me and Rudolf in the Netherlands and in just a month. So I'll also link the conference website. If you're listening and you're in time and you're not that far away, you feel yourself invited. It looks like a fun event and I've heard Angus will also be there, so you can take a copy of the paper on the rise of the euro class and perhaps get an autograph. Anyway, I kind of thought with the thoughts where to put this interview with Rudolf. I thought maybe we should put it in the experiments that change the fire science, but it's not really science. It's something that changed the engineering. I've decided to keep it as normal podcast episode, but definitely programs like this, developments like this, where a bunch of people get together in a room, they define a standard, then everyone works towards round robin, everyone works towards the calibration. Then there's a massive effort to compare this with a room corner facility. Even nowadays people are making PhDs comparing cone calorimetry with SBI, with room corner tests. It's still in use. It's still still today. New ways of using this method are being introduced, and that's that's really interesting. That's beautiful in fire science. This, this thing's never stopped. There was also an interview with Biggit Messerschmitt, which I also link in the show notes. She was also part of the program when they were comparing it with the room corner test. We also discussed testing regimes, testing methods, and I think it's great counterpart to Rudolph's interview. If this one interested you, I'm sure the Brigitte's one will be very interesting to you as well. So with this listening recommendation now, I'll just stop here with this episode. Thank you very much for being here with me and I am looking forward to see you here next Wednesday. Take care Bye. This was the Fire Science Show. Thank you for listening and see you soon.